The Equilibar back pressure regulator has only one moving part; therefore, the selection of the right diaphragm is a critical choice that is best made in consultation with our application engineers. There are many factors that must be considered to assure that the diaphragm is suitable for the application. Some of these factors include:
- Chemical compatibility
- Pressure rating
- Temperature compatibility
- Suppleness (improves sensitivity)
- Low Flow Performance, which is a function of
- Hardness (softer gives better low flow cut-off)
- Stiffness (gives better precision)
- Tendency to wrinkle in selected service (hurts low flow performance)
- Robustness (resistance to cutting or puncture in cyclic service)
- USP Class VI compliant
- Availability
There is often a balance between choosing a very thick conservative diaphragm and a thinner, more supple diaphragm that can offer more sensitive performance. Fortunately, for most applications, it is possible to select a diaphragm that is both highly sensitive yet strong and durable enough for the application. Equilibar’s application engineers have years of experience to assist you in this selection.
Chemical Compatibility
Equilibar specializes in selling products to the chemical research sector and our engineers therefore have vast experience working with harsh chemicals. Most of our diaphragms are highly resistive to attack from chemicals. Many applications are fulfilled with our proprietary PTFE/Glass reinforced formulation diaphragms; however, other options are available to meet specific needs.
For information regarding chemical compatibility between your chemicals and various diaphragms, we recommend the Cole Parmer Chemical Compatibility Database and this Stainless Steel 316 and 316L properties page.
Because Polyimide is not typically rated for use in chemical applications, Equilibar has conducted and made available its internal test results. See Polyimide diaphragm information page.
In many situations, metal diaphragms offer better performance for severe service conditions but they also have limitations that must be considered. See our metal diaphragm information page for detailed information.
Diaphragm Property Summary
Material | Relative Chemical Compatibility | Performance Considerations | Temperature/ Pressure | Robustness and Other Considerations |
---|---|---|---|---|
PTFE & PTFE-Glass | A++ | Excellent through wide range of flow rates | 150C for most applications. Up to 2500 psig (3000 max) / 172 bar(g) (206 max) | Reliable in most research applications |
Enhanced PTFE | A+ | Meets USP Class VI Specifications; | 150C temperature rating. Up to 150 psig / 10 bar(g) | Mechanically enhanced for improved creep and flex |
Hastelloy | A+ | Not for lowest flow ranges. Typically used for medium to high pressures, or to avoid H2 permeation | Good for max temperatures and pressures | Excellent for avoiding permeation |
Stainless Steel 316L | A | |||
PEEK | A- | Very good through wide flow range | Excellent for pressure range, limited use above 100C | Excellent choice for chemicals without excessive temperature |
Polyimide | B- Good for hydrocarbons and fuels; | Very good through wide flow range | Up to 300C and 5000 psig / 344 bar(g) | Superior robustness in many applications, including high temperature |
Polyethylene (LDPE) | B- | Excellent for ultra low and low pressures | Low temperatures, pressures below 100 psig / 6.9 bar(g) | Robust for low pressure applications only |
Viton (FKM), reinforced | A- | Excellent through wide range. Superb low flow performance. | Up to 150C, typically up to 1000 psig / 69 bar(g) | Rubbers have the best combination of both sensitivity and robustness. |
Buna Nitrile, reinforced | B- | Typically up to 100C, typically up to 1000 psig / 69 bar(g) | ||
EPDM Rubber, reinforced | B- |
Note: This reference information is presented as an informative guide for most applications but cannot be considered an exhaustive list or an absolute specification. Pressure, temperature, and chemical exposure all work together to impact diaphragm life, and not all combinations of these factors can be used simultaneously. Consult an application engineer for diaphragm service recommendations. It is necessary that end-users take responsibility to avoid the possibility of injury or property loss in the event of an unexpected leak or diaphragm failure.
How Equilibar Evaluates Diaphragm Materials
Equilibar engineers study diaphragm performance in three important ways.
- Short-term, Room Temperature Burst Testing : We study the burst pressure over several orifice sizes to determine the strength of the material and project the burst pressure in commercial regulators
- Temperature De-rating Burst Testing : We study the degradation of burst strength of the material at various elevated temperatures to roughly estimate a temperature derating factor. Our internal data is compared with published data where available.
- Performance Testing : We run performance trials with various diaphragm materials to know where best to apply them. This includes determining the lowest flow achievable with any particular material.
Service Factor
The “service factor” of the diaphragm is considered to be the ratio of the expected short-term burst pressure (adjusted for any temperature de-rating factor), divided by the maximum rated operating pressure. For most materials, a service factor of 4 to 5 would be considered quite adequate, while other materials subject to fatigue, might require a much higher service factor.
Equilibar regulators are typically rated to the application requirements with both the requested operating range and the diaphragm service factor in mind. The specifying application engineer will typically try to retain the highest service factor possible, while meeting the required sensitivity and accuracy.
For example, if an application has no low-flow sensitivity demands but has a high pulsating cycle load or a potential for particle contamination, the specifying engineer might select a thicker rubber diaphragm with a service factor of 10. Such additional strength and thickness can serve to lengthen the service life of the diaphragm and help it withstand abrasion and wear over time, while not negatively affecting precision.
In a different application, a researcher might require a 1000:1 flow turn-down ratio and a 100:1 pressure set-point ratio. Such wide ranges in flow coefficient are typically not available from competitive regulators, and the absolute priority is on the demanding precision and low-flow performance. The application engineer might select a diaphragm with a 4:1 service factor, explaining that the diaphragm may need to be replaced periodically if aggravating factors (such as debris, abrasion, chemical attack, or severe pulsations) are present.
Contact an Equilibar Application Engineer for Support
Equilibar has years of experience working with various diaphragm materials in a wide range of application parameters. Equilibar encourages you to contact one of our engineers to discuss your application’s particular requirements.
If your diaphragm fails in service unexpectedly, be sure to contact your application engineer for support. Where needed, we can often ship replacement materials the same day. In many cases, we can learn from photographs of the failed diaphragm and recommend a better material for the service.
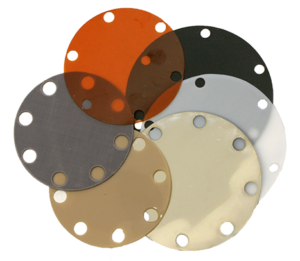
Assortment of Equilibar diaphragm materials