What to consider when choosing back pressure regulator?
A common dilemma is how to choose the best pressure control method for a process. Pressure control devices differ in mechanical design, type of operation and sensing method. There are spring-loaded valves, dome-loaded valves and air-loaded valves, for instance. Depending on the application, using one or the other may be advantageous.
What is a traditional spring-loaded valve?
Traditional spring-loaded valve provides reliable pressure control for most simple processes. In this design, a compressed spring is the loading mechanism that balances force against pressure on a diaphragm or piston. Small imbalances on the diaphragm or piston result in the valve opening or closing. It is easy to adjust with a screw or a knob, is self-operated and relatively small, which offers advantages. The disadvantage is that precision may be limited with varying flow due to the varying spring constant as the valve opens. Hysteresis can be an issue, causing overpressure problems.
How does a dome-loaded valve work?
A dome-loaded valve uses a fluid pressure, normally air, on top of a sensing element to provide the setpoint pressure. The sensing element is typically a diaphragm for lower pressures or a piston for pressures above 10 to 20 bar. In simple dome-loaded regulators, a single sensing element separates the process fluid from the dome fluid, and the pressure imbalance drives the valve position. The pressure of the fluid fed to the dome is set by a second regulator called a pilot regulator, which could be a manual air regulator for manual applications or an electronic pressure regulator for computer automated applications. The downside is the complex design needing two valves. The advantage of this design is improved precision and less hysteresis effects, so it is desirable to use where high precision is important.
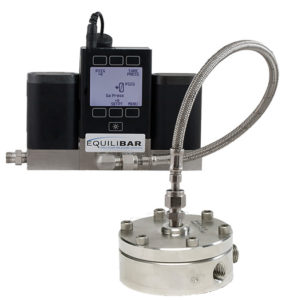
Equilibar dome-loaded valve has advantages of no hysteresis to improve precision
Back Pressure Valves (Regulators) from Equilibar:
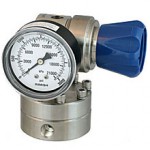
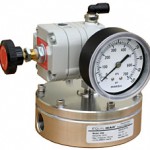
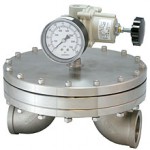
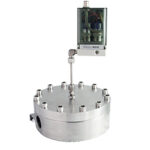