To control flow, the Equilibar flow control valve is configured in a flow control loop with an electronic pressure regulator, a flow meter and a logic controller. In the photo at right, an Equilibar FDO4 valve (lower right), is piloted by an EPR-150 (top right) in a control loop with a high resolution Bronkhorst Coriolis flow meter (left). Not shown is the PID control logic getting feedback from the flow meter and sending input to the EPR-150.
Equilibar sells flow control valves with high resolution electronic pilot pressure regulators to provide precision flow control with instantaneous response. The customer provides their own flow meter and PID controller to suit their process needs. For best performance, we recommend using a responsive flow meter and PID controller with guidance from an on-site controls engineer experienced in tuning feedback loops
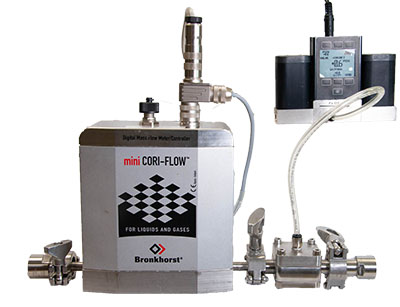
Equilibar FDO4 valve in a flow control loop with an Equilibar EPR-150 electronic pilot regulator and a high resolution flow meter. PID controller not shown
What are the primary flow control setups for Equilibar valves?
1. Control using an existing PLC and internal programming protocols:
Use a high resolution flow meter to provide feedback to a PLC. The PLC calculates and provides a command signal to an Equilibar electronic pressure regulator (E/P) to adjust the air pilot pressure to the Equilibar FCV. The customer’s on-staff programmer can tune the PLC settings to optimize the Equilibar FCVs performance for a specific application. See schematic below and the video at right.
Video: Equilibar flow control using a an existing PLC
2. Control using a Bronkhorst or similar flow meter with built-in flow control software:
The software built into a Bronkhorst or similar type flow meter can be used to provide an output signal to an Equilibar electronic pressure regulator (E/P). The software is easily accessible through a laptop computer. Use this software to optimize settings for each specific application. See schematic below and the video at right. Link here for even more details about flow control using Bronkhorst flow meter.
Video: Equilibar flow control using Bronkhorst mini CORI-FLOW meter with integrated control software
3. Control using LabVIEW, Arduino, or similar non-dedicated flow control software:
Use LabVIEW, Arduino, or similar technologies to send signals between I/O control boards, the flow meter and the Equilibar electronic pressure regulator. On-site personnel can tune the PID settings in this program to optimize the valve’s performance for each application. The end-user must develop the LabView instrument file or other program specific to their application. See schematic below and the video at right. Link here for even more details about using LabVIEW or Arduino for flow control.
Video: Equilibar flow control using LabVIEW
4. Control using an EQ-DA smart controller and its browser-based GUI:
The EQ-DA is a smart electronic pressure controller that runs its own internal PID loop. The customer’s existing flowmeter or other external sensor can be connected to the input of the EQ-DA and used as the process variable for the PID loop. On-site personnel can tune the PID settings using the associated browser-based GUI. Link here for even more details for using EQ-DA for flow control.