How dome-loaded pressure regulators are used for automated process control
Dome-loaded means that the setpoint to the pressure regulator is provided by a fluid (typically air) pressure on the top dome port. The fluid on the dome is controlled by a manual pressure reducing regulator (PRR) or an electronic pressure regulator. Dome-loaded pressure regulators, coupled with EPRs provide comprehensive computer control to a process liquid, gas, or mixed phase stream.
This approach has certain advantages over traditional pressure control valves which typically have a delayed response time, limited flow ratios, and depend on PID loop tuning. On the other hand, large chemical plants rely on traditional pressure control valves due to economic scale factors.
Dome-loaded pressure regulators come in both “back pressure” or “pressure reducing” varieties. Back pressure regulators control their inlet pressure and open to reduce upstream pressure. Pressure reducing regulators control their outlet pressure and open to increase downstream pressure (see more about the differences). Equilibar sells back pressure regulators.
Read more about how dome loaded regulators are used for precision fluid control in our article published in Water Technology Magazine.
Equilibar dome-loaded back pressure regulators
Equilibar dome-loaded back pressure regulators (BPRs) have a ratio of 1:1 between the dome setpoint pressure and the controlled inlet pressure and are used in complex automated process control applications around the world. When coupled with an electronic pressure controller, Equilibar patented BPRs can provide precise automated control for difficult processes. In the image to the right you see a plot of a fluid pressure emulating cardiovascular pressure. The actual liquid pressure is yellow; The target waveform is red. An Equilibar BPR is set up in a recirculating loop with control configuration emulating cardiovascular pressure using a pulse wave input into an electronic pressure regulator, or electropneumatic (E/P) controller. See Schematic below.
Some example applications are shown below and more application examples can be found on our applications pages.
Dome-load Back Pressure Regulators
Liquid Pump Application
The schematic above shows how a dome-loaded back pressure regulator can be used to control the flow rate to a dispensing application. Instead of using a complex variable speed pump, the output pressure of any type of pump can be controlled by the BPR, which allows only enough fluid to return to the supply vessel as required to limit the dispensing pressure. The PID flow control loop controls the signal to the electronic pressure regulator, which thereby controls the set-point of the dome-loaded BPR with an air pressure signal.
While this example does use a PID flow controller, the reaction time of this system is infinitely faster than that of a PID controlled control valve. That is because the control valve action has to swing suddenly with every change in dispensing flow rate. However, the BPR will hold the header pressure constant without any change in controller output. The PID is therefore only used for small adjustments to the header pressure, and can be tuned slower while also enjoying instantaneous reaction from the regulator.
Dome-loaded Back Pressure Regulators
Gas Reactor Application
The schematic above shows an electronic pressure regulator and a dome-loaded back pressure regulator controlling the pressure of a laboratory reactor, such as might be used in catalyst research. Two separate Mass Flow Controllers (MFCs) are used to inject reactants in the vessel. The vessel pressure is monitored by the process computer. The pressure in the reactor is commanded by the computer through an electronic pressure regulator, which produces an air or nitrogen pressure signal to the dome-loaded BPR. The BPR allows only enough gas to escape from the reactor to maintain the precise desired pressure setting.
Learn more about Equilibar’s ultra sensitive dome-loaded back pressure regulators .
Learn about electronic pressure regulators from Equilibar.
Contact our engineers to discuss your application.
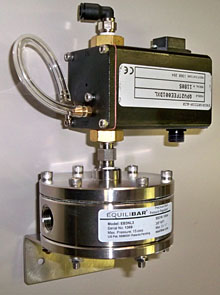
An Equilibar dome-loaded back pressure regulator (bottom) is commanded by an Equilibar QPV electronic pressure regulator (top) to provide complete process automation.
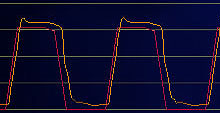
An example of medical fluid pressure control emulating cardiovascular pressure by using a dome-loaded back pressure regulator. Actual liquid pressure is yellow; target waveform is red.