It’s been more than 30 years since I moved to the mountains of Western North Carolina, but the beauty of this place continues to make me happy every single day. I’m grateful that I’ve been able to volunteer for organizations that protect our natural resources and I’m honored that here in our community, I’m known as an environmentalist and conservationist.
Of course, I’m also the owner of a manufacturing company and I fully realize the tension that exists between working profitably and working sustainably. I think the key to this dilemma is to constantly look for efforts that will make a positive difference. Even small changes add up to make a big impact.
I’m especially thankful for the sustainability efforts that several of our team members have initiated this spring and summer.
In May, Production Manager Sam Sematis spearheaded a project to switch from using paper coffee filters to using permanent mesh filters. If you’ve seen how much coffee the Equilibar team drinks, you know that this project is saving a lot of paper, plus providing some great compost for summer gardens.
In June, David Reed, Vice President of Operations, oversaw the replacement of our wasteful and temperamental HVAC system with units that are much more energy efficient and environmentally friendly. It was great to work with Horizon Heating and Air Conditioning, a local company that has occasionally been patient and creative enough to serve as a sounding board for some of our refrigeration application ideas. David is also overseeing the process of replacing inefficient windows and adding insulation around the facility. All these changes not only conserve energy, but also save money and create a more comfortable work space.
Finally, Todd Wiles, who takes care of maintenance for Equilibar, has been overseeing an ongoing project to replace the lighting units in the office areas of our facility, switching from fluorescent ballast lighting to LEDs. This will create significant energy savings.
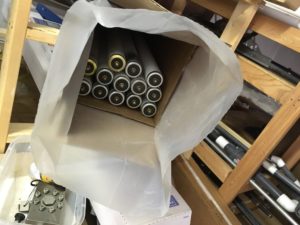
These fluorescent bulbs are being sent for safe disposal in a box that protects against mercury exposure
Disposing of fluorescent bulbs is tricky because they often break when put in the garbage and release mercury and other nasty toxins into the environment. Even so, throwing fluorescent bulbs in the trash is standard procedure for businesses in our area because they are not advised to do anything else. We are spending money to try to do better. Instead of just tossing the old bulbs, Todd has been carefully collecting them and sending them to a recycling center in specially designed containers that prevent the mercury from leaking. This also enables components of the bulbs to be recycled rather than end up in the landfill. We believe this project is important enough to take the extra time and money to do it right. Thank you, Todd!
For me personally, Equilibar’s most exciting applications are the ones that involve clean energy and other environmental efforts. It’s gratifying to play a technical role in improving our world, but it’s also great to do the small things we can do in our own space. I am hopeful about our future and will always be on the look-out for ways to work more sustainably.