Active Pharmaceutical Ingredients (APIs) refer to the substances in pharmaceutical products that deliver the actual therapeutic activity—in other words, the API is what treats, mitigates, prevents or diagnoses disease. In a painkiller capsule, for example, the API would be the substance that treats pain. The rest of the capsule would be composed of inactive substances such as mineral oil or cellulose. These are called excipients.
APIs come in the form of liquid, powder, crystals and extracts. They are manufactured through chemical and physical processes, which can include a complex series of steps involving a range of technologies such as chemical synthesis, plant extraction or biotechnology.
To make a pharmaceutical end product, the API is combined with inactive excipients to form the tablet, serum or other medication that is sold to the public. Common medications made through API processes are ibuprofen, loratadine, metoprolol and antibiotics.
Vacuum Drying Techniques for API
API ingredients used in a powder or crystalline form require drying after purification. This is one of the final steps in the manufacturing process and is used to remove excess water. Drying techniques include spray drying, lyophilization (freeze drying), and vacuum oven drying. Freeze drying is used to preserve biologic material and includes a vacuum drying step after freezing.
Vacuum ovens are used to dry pharmaceutical ingredients to avoid high temperatures that could damage or degrade the product. The low pressure reduces the vapor pressure and allows drying at a lower temperature. Vacuum conditions can also help remove entrapped liquid and obtain low moisture content and can serve to remove solvent from the system.
Because of the high dollar value and sensitivity of the pharmaceutical ingredients, as well as government regulations, it is important to have careful control over the processing. Most of the processes are automated to ensure high quality and efficient operations. Process automation, precision vacuum control and the ability to handle chemicals are important design factors in API vacuum drying.
A dome-loaded multiple orifice vacuum regulator, such as those offered by Equilibar, is a good solution in this application. The EVR reacts instantaneously to any process fluctuations to keep the vacuum pressure in the dryer at its intended setpoint. It can be constructed with materials to handle volatile chemicals coming from the product and can be automated using an electronic pilot setpoint regulator. A detailed application example can be found here.
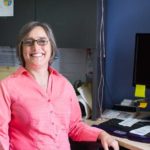
Diane Jacober, M. Eng
As always, we invite you to contact an Equilibar application engineer to discuss vacuum control, API processing or any other pressure or flow control questions you have.
We look forward to hearing from you!