Viscous fluids and fluids with particulates can plug small orifices inside a valve, making it difficult to operate properly. Particles can also be abrasive, causing damage to the internal parts of a valve.
The main body of an Equilibar regulator has multiple parallel orifices through which the fluid flows. Pressure is controlled from above with a supple diaphragm which is the only moving part. As fluids travel through the regulator, the diaphragm lifts and lowers to allow flow through some or all of the orifices depending on the pressure setpoint. Pressure setpoint is determined by a “pilot pressure” of air or other fluid on top of the diaphragm. As flow and pressure conditions change, the diaphragm responds.
The regulator body and diaphragm can be fabricated with materials to withstand abrasive fluids or any other temperature or chemical compatibility concerns. This flexibility allows the Equilibar valve to handle viscous fluids as well as fluids with particles. And because of its simple design, it is easy to disassemble and clean the orifices if the flow path does become blocked
Case Study: Firsthand account of Equilibar performance with particles in fluid
A long-time Equilibar customer in Germany, Anton Nagy, wrote a case study about a catalysis application where rust had formed in the process lines during an unexpected disruption. When the process lines were disassembled for maintenance, the customer found that rust had accumulated in some of the process equipment, including in the orifices of the Equilibar valve body. They cleaned the valve, put it back into service and it continued to work.
“To our amazement, the Equilibar valve continued to work after just flushing the system with nitrogen and a small amount of water.” This easy repair was possible because the large orifice size of the holes in the Equilibar makes them easy to clean and less prone to blockage. “Because of this, the feed-section of the (catalysis reactor) unit could be purged and immediately started back up,” Nagy said. “It wasn’t even necessary to change the stainless steel diaphragm.”
In this case, the Equilibar valve was designed to provide flow control for a high temperature monomer reactor which normally would not expect to experience particulate flow, but the Equilibar valve with its multiple orifice design and fast acting diaphragm is well suited for such cases when needed.
For more information, please contact an Equilibar application engineer to discuss your specific process.
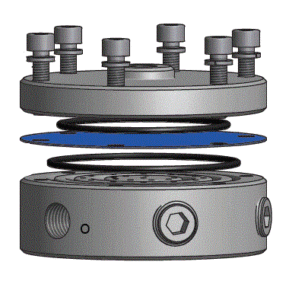
Unique Equilibar design with multiple orifices and flexible diaphragm results in excellent control of viscous fluids and fluids containing particles