Lithium-ion (Li-ion) batteries are the preferred energy storage solution for many applications, commonly used in smartphones, laptops, and even some electric vehicles. These batteries work by moving lithium ions between two electrodes – one positive and one negative, during charging and recharging cycles, enabling the storage and release of energy. Like many other battery types, there are several steps that go into the production of lithium-ion batteries.
Contact Equilibar to Discuss Your Vacuum ApplicationHow is vacuum used in battery manufacturing?
The first part of building a battery is manufacturing the electrodes. To do this, metal foils are coated in slurries of different materials – typically something like lithium cobalt oxide or lithium iron phosphate for the cathode and graphite for the anode. When preparing these slurries, the graphite or metal oxides are mixed along with various solvents and binding agents. This mixing can take quite a while with a thick slurry, which often leads to entrained air bubbles in the mixture. As such, vacuum is typically applied to the mixing tank – this causes any entrained gas bubbles to expand and rise out of the liquid, leaving behind a homogeneous paste.
Once the electrodes are coated in this paste mixture, they’re typically put in a vacuum oven. This time vacuum is applied to boil off any residual solvents and leave behind only a solid coating of metal oxide or graphite on the electrodes.
After the electrodes are made, they are assembled in a cell- typically either stacked or wound together with a separator between them. This separator material is porous and filled with a liquid electrolyte solution that facilitates the movement of lithium ions between the anode and cathode.
When the batteries are filled with this electrolyte solution, it is important that they are degassed once again under vacuum conditions. Any entrained gas bubbles in the liquid can impede the movement of Li-ions, limiting the efficiency of the battery. Additionally, any other contaminants from previous manufacturing steps that may be present like residual solvents must be boiled off. The purity of the battery chemistry is absolutely crucial to ensure optimum performance and longevity of the batteries.
After the battery cells are filled, they are vacuum-sealed. Typically, this is done with a plastic wrapping which ensures that each cell is safely contained and free from any environmental contaminants or moisture. Below is a schematic that shows some of the vacuum applications in battery production and how an Equilibar EVR vacuum regulator can be used to control the process.
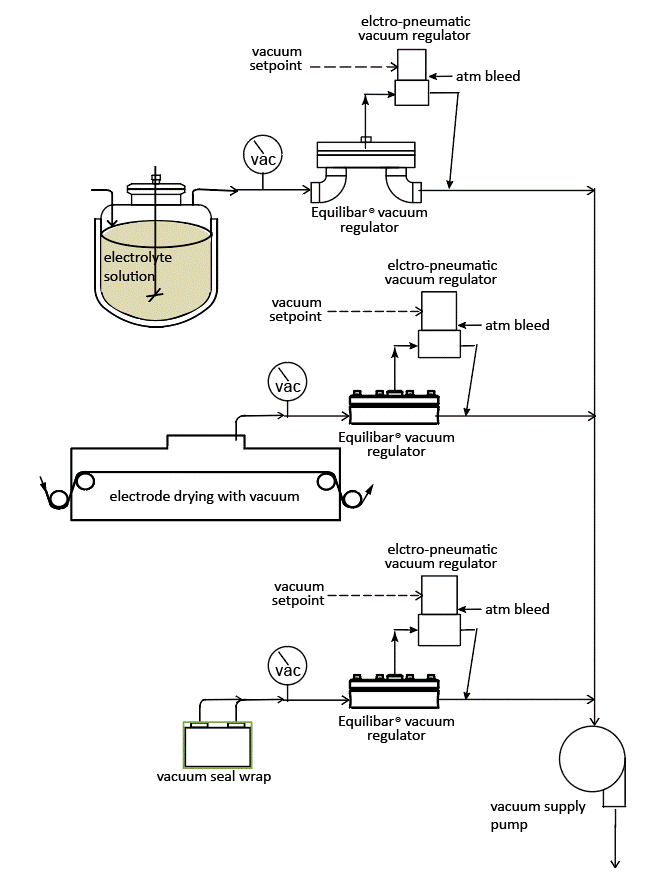
Schematic of three vacuum applications in battery production where Equilibar vacuum valves are used
Why is Equilibar the best vacuum control solution for battery manufacturing?
Vacuum comes into play during several steps in the battery manufacturing process. These steps are crucial in maintaining a final product that is safe and efficient. However, vacuum processes during Li-ion battery production can present some challenges:
- Chemical compatibility – this is particularly important during the electrode slurry and electrolyte degassing steps, as any solvents present may be chemically corrosive. The simple design of Equilibar® EVR vacuum regulators makes them easy to customize the using materials of construction for aggressive chemistries. PTFE, FKM, and FFKM are standard materials for soft seals in Equilibar vacuum valves, with other materials available upon request. Most Equilibar valves use SS316/SS316L body materials, but the body can also be easily changed to other alloys or even polymers if needed.
- High temperatures – during the vacuum drying step the oven may reach temperatures of up to 250 °C. Equilibar valves are easily customized for these temperatures, with polyimide diaphragms and Kalrez O-ring options being suitable for up to 327 °C.
- Wide, variable flow range – during the multiple degassing steps, the amount of flow required will vary quite a bit. There will be an initial rush in of gas through the vacuum line when first applied, with the mass flow gradually decaying as more and more bubbles move their way out of the liquid. Equilibar vacuum valves have incredibly wide operating Cv ranges, with turndown ratios of 10,000:1 possible on all of our valves. This means they can maintain a stable vacuum level across a very wide range of flows.
- Precise control – during the electrolyte degassing step, very precise vacuum is required, oftentimes with stability of <1 mbar needed. If too much vacuum is applied, the electrolyte may be pulled out of the cell or splatter. If too little vacuum is applied, bubbles will remain in solution. Equilibar vacuum regulators allow for incredibly precise control across a wide flow range. When coupled with an electronic pilot and closed loop control, accuracy on the order of fractions of a torr is readily achievable.
RELEVANT PRODUCTS
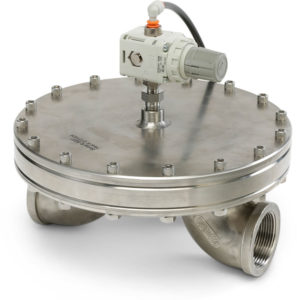
Equilibar EVR-BD12 1.5″ vacuum valve with wide Cv range
Download a BrochureRequest a Quote
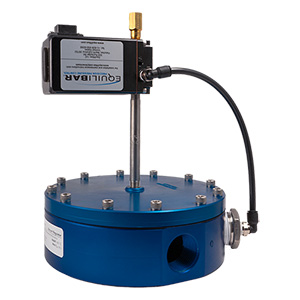
Equilibar EVR-GSD8 1″ vacuum valve in Anodized Aluminum with electronic pilot regulator for automated control
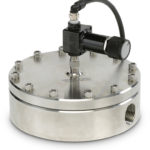
EVR-GDS4 1/2″ vacuum regulator in stainless steel
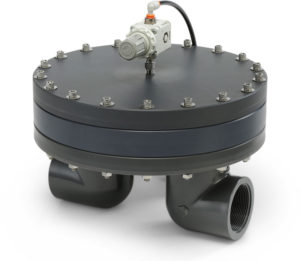
EVR-BD16 2″ vacuum regulator in PVC
Download a BrochureRequest a Quote
JOURNAL ARTICLE
Article from June 2020 Processing Magazine
Controlling chemical vacuum processes with direct sealing diaphragm valves
Due to the hazards involved with corrosive chemicals, process components must be chemically compatible, as well as extraordinarily accurate and precise. Traditional methods of controlling vacuum are not always suitable, and alternatives–including direct sealing diaphragm valves– must be considered.