The bonding process typically requires precise pressure control for a long duration across a large area. The specifications for a vacuum bagging process can be very detailed and in many cases data will be collected during the process for quality control. During this time, there is a chance the vacuum pump could experience spikes or dips. The use of an Equilibar® vacuum regulator (EVR) is an excellent solution in vacuum bagging systems to avoid disturbances in pressure over time. The EVR responds instantaneously to changes in pressure and adjusts accordingly to keep a precise vacuum setpoint regardless of perturbations in the vacuum. Another advantage of using an Equilibar EVR in this instance is that it can be designed using a variety of chemically compatible elastomers and metals.
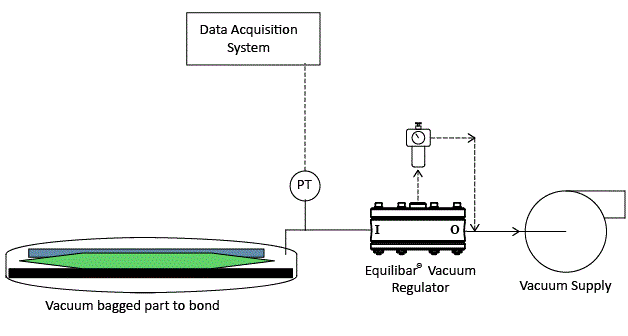
Equilibar EVR with manual control used for precision vacuum control in vacuum bagging process
Automated Vacuum Bonding
For vacuum bagging applications that require automation for ease of use on the shop floor, the Equilibar EVR is very easy to automate. Instead of using a manual pilot regulator to control the setpoint of the EVR, an electronic vacuum regulator can be installed. A vacuum setpoint can be dictated by an external supervisory control device sending a 4-20mA or 0-10V signal to the electronic vacuum regulator. The EVR will keep precised control at the pressure sent through the electronic E/P vacuum regulator. See schematic below.
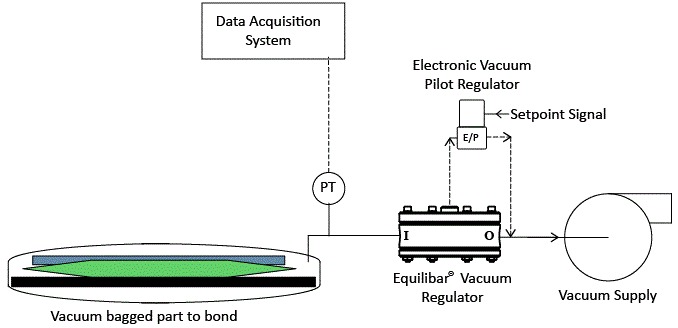
Electronic pilot control of an Equilibar EVR assists with automation
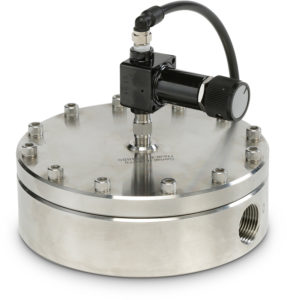
Stainless Steel Equilibar EVR-GSD6 with manual pilot controller
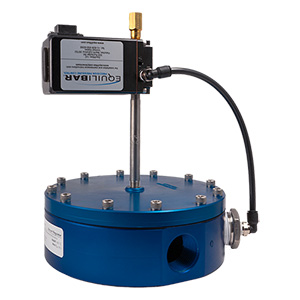
Anodized Aluminum Equilibar EVR-GSD6 with a QPV electronic pilot controller
Application Spotlight: Vacuum Bonding for NASA
The NASA contractor building the Orion spacecraft uses a vacuum bonding process to secure all the Thermal Protection System (TPS) to the aeroshell of the craft. The aeroshell protects the vehicle and crew from thermal loads during reentry. Every tile and Avcoat block is vacuum-bonded onto the Artemis 1 and Artemis 2 spacecrafts. They use Equilibar EVR regulators because of their ability to maintain bonding pressures within tight engineering tolerances. These EVR regulators play a critical role in TPS processing. The largest bonding surface is just over 16 feet in diameter. The NASA contractors build a vacuum bag across the entire 16 foot surface, so it’s a challenging application. Read more about the use of Equilibar EVR for the NASA Artemis program in the feature article to the right.
- Explore Product Details for Equilibar’s EVR Vacuum Regulators
- Learn more about how Equlibar® vacuum regulators work
- Contact an application engineer to discuss your vacuum application.