High Speed Evaporator Temperature Control
A novel method is available to make very fast and precise temperature changes to the evaporator surfaces directly. By using an electronically actuated back pressure regulator downstream of the evaporator it is possible to maintain the coil temperature exactly at the refrigerant saturation temperature corresponding to the controlled fluid pressure.
During modulating heat transfer conditions, two-phase (saturated vapor + liquid) refrigerant will pass into the back pressure regulator (BPR) and expand into vapor inside the valve. When maximum cooling is needed, the BPR opens, dropping the evaporator pressure and allowing maximum evaporation in the coil. As the pressure setting is reduced, an immediate boost of cooling is obtained from the latent heat of the liquid rapidly vaporizing on the tube surfaces. The process control benefits from both the dynamic evaporation boost as well as the steady state heat transfer control.
Video demo of Equilibar B6R in evaporator pressure control
Contact an Equilibar application engineer to discuss how two-phase refrigerant control can be adapted for your critical and demanding application.
Enhanced Load Control With Variable Expansion Valve
Most vapor compression systems or refrigerant systems use an expansion valve to generate a temperature drop in the fluid stream. This temperature drop cools the evaporator coil, which allows for heat extraction of the desired cooling space. Traditional expansion valves were fixed orifices or Thermal Expansion Valves (TXVs). The TXV allows for the user to control the temperature and pressure supply to the evaporator coil. However, this device can be dramatically improved with the Equilibar 2-phase precision control Back Pressure Regulator (BPR). By replacing this TXV valve with an Equilibar BPR, the user is now able to control the dP across the expansion valve in the system, thus controlling the quality of the fluid at the outlet of the condenser.
This control is further improved by adding an electronic pilot. This closed loop system then allows for a variable condenser pressure, which not only provides infinite dP control over the system but can also provide system capacity control. The electronic pilot of the Equilibar has high speed response and allows the system to operate more efficiently by changing the heat load differential from evaporator to condenser. If flow control is preferred over pressure control, the Equilibar BPR can also be set up in a flow control loop.
Equilibar back pressure regulators excel at processing both two-phase and phase-change fluid streams. The expanding refrigerant vaporizes in the outlet ports of the back pressure valve, maintaining the inlet port (and thereby the compressor outlet) at the desired pressure for optimum efficiency.
In this particular example, a two-loop electronic pressure regulator has been selected. This device monitors a remote sensor and makes any necessary adjustments internally to keep the sensor right at the desired operating pressure. If such a sensor is not desired, a more economical solution would be to have the E/P operate directly from the controller in response to other variables.
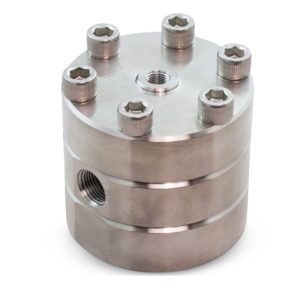
Equilibar B6R back pressure regulator is designed for use with supercritical CO2 applications such as evaporator refrigerant pressure control
The Equilibar® back pressure regulator works in a unique way and its multiple orifice design is capable of maintaining precise control even with uneven slugs of vapor and liquid enter the valve.
By coupling the Equilibar BPR with one of our high speed electronic pressure regulators to provide the variable setpoint, a high speed temperature control system can be adapted for critical processes.