Spraying systems may have a single nozzle or a manifold of many nozzles firing to cover the surface of the product to be coated. To perform properly, they require consistent nozzle pressure and careful nozzle valve timing.
One key challenge in spray coating systems is handling the rapid change in flow rate during start-up and shut down. For example, if a spraying line has a dozen parallel nozzles, it might take several seconds during machine start-up for each of the positions to become active as the items being sprayed move down the conveyor line. The opposite situation occurs at machine shutdown as the conveyor slows down and the last item passes under the spray nozzle manifold. During these ramping up and down times, the amount of flow through the spraying line can vary dramatically.
Accurate pressure control at the nozzle manifold is crucial to optimize throughput and achieve a consistent coating. Too little pressure and there will not be enough flow through the nozzles, leading to a weak spray that may not properly coat the item. Too high a pressure and there will be an excess of flow through the nozzle, wasting product.
High Speed Pressure Control for Spraying Systems
For challenging spraying applications, one solution is to install a high-speed back pressure regulator near the exit of the nozzle manifold, as shown in the schematic below.
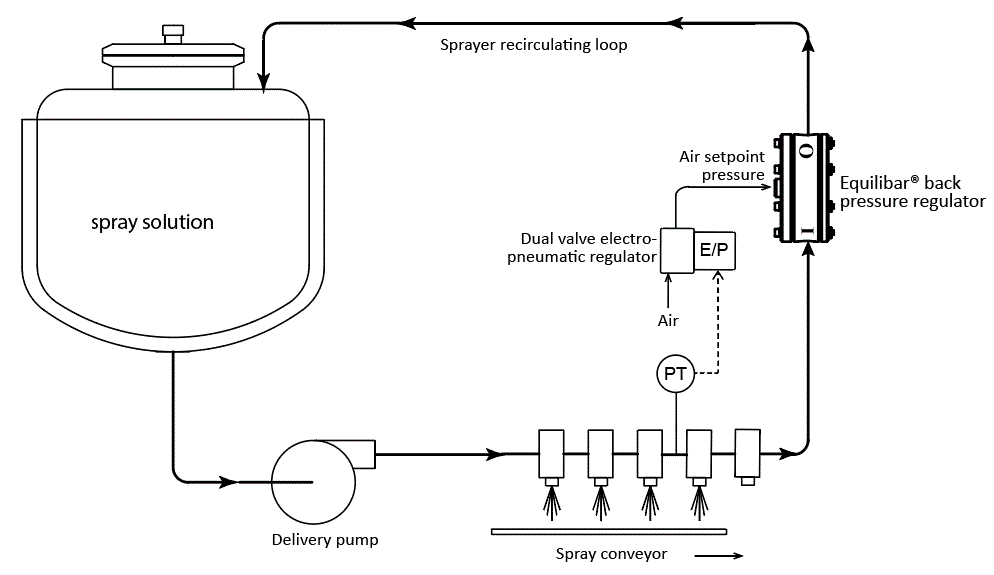
Schematic of an Equilibar high speed back pressure regulator at the exit of a nozzle manifold to control manifold pressure for efficient spray coating
The primary requirement for this approach is to install a circulation line back to the inlet of the pump. While this is sometimes complicated, the advantages can be significant for applications experiencing persistent pressure fluctuations.
The Equilibar back pressure regulator is a high precision device that responds in approximately 1 millisecond to pressure changes at its inlet. The speed and precision are driven by the use of compressed air as a 1:1 pilot setpoint signal to a supple diaphragm on top of multiple parallel orifices.
Learn more about how the Equilibar BPR worksIf the BPR can be mounted extremely close to the manifold, it may be possible to run with a fixed air pressure pilot. For example, to control the manifold at 2 bar pressure, a 2 bar air pressure signal would be supplied to the dome of the BPR.
However, for many applications, such as viscous fluids or installations where the BPR is not located directly at the manifold, a dual valve electro-pneumatic pressure controller would be recommended (as shown above). This closed-loop approach assures that the manifold pressure sensor sees the desired pressure by making slight adjustments as needed to the pilot pressure on the dome of the BPR to offset friction effects throughout the system.
Contact an application engineer for more information.
Application highlight – Spray coating viscous industrial coatings
Spray coating industrial substrates such as molten glue coatings, metal coatings, or other challenging fluids with high viscosity or that contain some solids is difficult. Fluids with particulates and viscous fluids have the potential to plug small orifices inside a valve, making it difficult for them to operate. An Equilibar BPR, however, has a flow path with multiple parallel orifices. The simple and robust design lends itself to applications with solid particles. Bodies can be made from hardened materials for abrasive particles, and, because of the BPR’s simple design, it is easy to disassemble and clean the orifices if the flow path does become blocked.
Contact an Engineer to discuss your application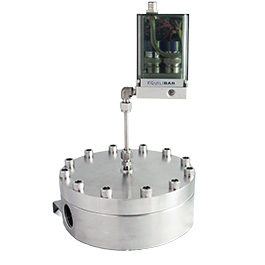
Equilibar GSD8 1″ back pressure regulator with electronic pilot can be used for high speed industrial sprayer control
Application Highlight: Egg Wash Pastry Coating
Many baked goods like pastries or cookies are coated in an egg wash, a mixture of beaten eggs, sometimes along with water or milk. Coating an item with an egg wash prior to baking produces a shiny golden-brown color in the finished product and helps additional toppings or coatings adhere.
Egg wash spray coating presents several challenges. In addition to the variable flow rates during start up and shutdown as described above, the egg wash mixture is often somewhat viscous. After the spraying is completed, the entire line may also be subjected to a clean in place (CIP) cycle and flushed with a high temperature cleaning solution to ensure there is no egg mixture left in the piping.
Equilibar valves handle high viscosity fluids very well, having been used to control pressure of fluids with viscosities of over 50,000 centipoise. The Equilibar FDO sanitary BPRs are designed specifically for food & beverage, pharmaceutical and other sanitary processing. They have a crevice-free drainable design compliant with American Society of Mechanical Engineers (ASME) Bio Processing Equipment (BPE) standards, which allows for easy CIP cleaning. The FDO valves use enhanced PTFE (Jorlon) diaphragms, which can handle the high temperatures typically used during these cleaning cycles.
Equilibar engineers are highly experienced at designing systems for this type of demanding application. Contact an engineer today to discuss your spraying automation challenges.
How Equilibar high speed back pressure regulators can reduce cost
The payoff in savings for fast spray nozzle pressure control can be very large. Imagine a 2-meter-wide gourmet cookie conveying line moving at 1 meter per second. For a 3” diameter cookie, each lineal meter of conveyor can hold 288 cookies (24, 3” diameter cookies across the belt x 12 cookies along). If the conveyor speed is 1 meter/second and it takes 2 seconds for a traditionally controlled sprayer system to gain pressure control at the start or stop, that would represent 576 cookies with less than the specified egg wash coating at each start-up and shutdown, for a total of 1152 cookies.
If a company sells gourmet cookies in packages of 12 for $7.00, that ends up being 96 packages (1152/12) of cookies that can’t be sold for a total of $672 (96x $7.00) in lost revenue. If a typical gourmet cookie gross margin is 30%, that adds up to $470 in wasted product each time the conveyer starts and stops.
Assuming one batch of cookies is manufactured every 8 hours and the plant runs 2 shifts a day for 340 working days a year, the lost revenue and waste is significant. That lack of precise spray pressure control at start-up and shutdown translates into $456,960 in lost revenue [(2 shift x 340 days) x $672], and $319,872 of waste [(2 shift x 340 days) x $470.40].
Contact an Engineer to learn how Equilibar can help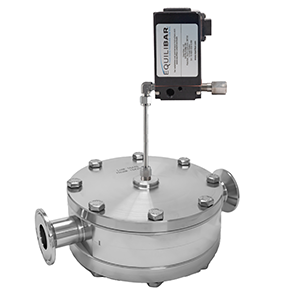
Equilibar FDO8 Sanitary BPR with an electro-pneumatic pilot regulator for high speed sanitary sprayer control