In bioprocessing operations using hollow fiber filters, transmembrane pressure across the filter (TMP) is the key driving factor for all other process variables, from feed flow strategies to permeate makeup flow in diafiltration.
Equilibar Engineer, Ryan Heffner PE, conducted extensive studies in TMP control methods to show how Equilibar® back pressure regulators offer improved precision to TMP control methods for more stable on-target control. His work demonstrated how on-target control impacts unit operations from protein denaturing to operating time.
General concepts of Ryan’s research are outlined below, and a recording of his presentation at BioProcessing International West in March is available upon request. Contact us to discuss your TFF system.
Contact Us Request Ryan’s Presentation
Fluid Mechanics Basics in TFF:
Fluid mechanics establishes the critical filtration performance, for which TMP is the main variable. Four essential components in a tangential flow filtration system are the pump, the filter, the valve or restriction, and the control loop. Component choices and control strategies need to work together to maintain TMP control at an optimal setpoint.
1. Filter fluid mechanics to consider
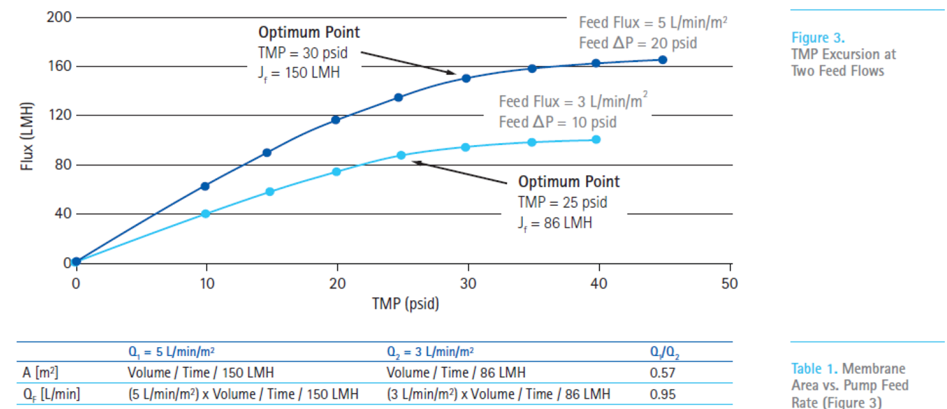
Huter, M.J., & Strube, J. (2019). Model-Based Design and Process Optimization of Continuous Single Pass Tangential Flow Filtration Focusing on Continuous Bioprocessing. Processes. Available: DOI:10.3390/pr7060317
- As TMP increases, change in flux diminishes.
- Higher TMP accelerates filter membrane fouling.
- Filters have an “optimum” TMP where flux is maximized and membrane fouling is minimized. The goal is to maintain this optimum TMP during the filtration process.
Feed Flow Considerations
- Ensure sufficient supply flow to the filter, greater than the permeate flow, which is entirely set via TMP pressure.
- Avoid excessive feed flows to keep shear within the hollow fiber in an appropriate range for the pharmaceutical being manufactured.
- If single-pass filtration is used, feed flow must also consider flow needs of other unit operations downstream
- Know the pumps fluid behavior – how is feed flow affected by head pressure, and what is the relationship between RPM and flow
- Manage your control strategies when using pulsating pump sources: Consider loop speed and signal aliasing in PID feedback to avoid runaway conditions.
- Ex: Graph below shows how sampling rate in a pulsating wave output can upset the PID loop and destabilize the control.
Pump Fluid Mechanics
- Flow is related to pump RPM
- Flow profile is determined by the pump type: sample graphic below
- Fluid mechanics changes depending on the flow profile
- As flow fluctuates, control mechanisms (pump, pinch valve or SDO valve) adjust to maintain setpoint
Control Loops in TFF
Component choice in tangential flow filtration systems is important when choosing a control strategy. The control loops in this study used three different control components: 1. Pump-controlled flow; 2. Flow control loop using Equilibar SDO back pressure regulator; and 3. Flow control loop using a pinch valve flow restrictor
- Pumps use variable frequency drive based on flow meter feedback to control flow to the filter
- Pinch valves adjust cross-sectional area, restricting flow from the filter to manage pressure for TMP control
- Equilibar SDO adjusts reference setpoint pressure directly proportional to pressure fluctuations to keep TMP stable
- Control loop speed and signal aliasing create complex feedback loops in pump-controlled flow loops
Experimental Results for 5x Ultrafiltration Unit Operation
A lab experiment was set up to test the TMP control performance of an Equilibar SDO single use back pressure regulator and a standard pinch valve. The components included a single-use centrifugal pump, Pendotech single-use pressure sensors, a Midikros filter with an SDO or pinch valve in the retentate line at the outlet of the filter to maintain TMP at 10psig with a feed flow of 150 mL/min. Water was the fluid used in this experiment. Below are the charts showing TMP measurements during the operation using the 2 control devices.
Experimental Results of Benchtop 5x Concentration IgG
In a final comparison of the control elements, the pumps and valves were used in a Repligen KMPi Benchtop system to process IgG to a 5x concentration at a TMP of 5psi. The Equilibar dome-loaded single use SDO valve saved 18 minutes (out of 117 total) over the pinch valve and peristaltic pump. This represents a 15% improvement.
Conclusions
The study concluded that the selection of components in a TFF system can have a dramatic effect on the efficiency of the TMP control method. Choosing compatible, responsive components can save time and money. Equilibar single use back pressure regulator self-regulates without a PID control loop which can eliminate out of control situations.