Back pressure regulators (BPRs) play a key role in several types of coretests such as core flooding and pore pressure transmission.
Core Flooding
Core flooding experiments are routinely performed in hydrocarbon reservoir engineering to investigate multiphase flow characteristics of rock-fluid systems. For such experiments, representative rock and fluid samples for a hydrocarbon reservoir are collected. The fluids are then injected through the rock under high pressure and high temperature in a laboratory setting. The results of core-flooding experiments are useful in forecasting the outcome of various injection/production processes that a hydrocarbon reservoir may undergo. A back pressure regulator is placed downstream of the core sample reactor to maintain the overburden pressure.
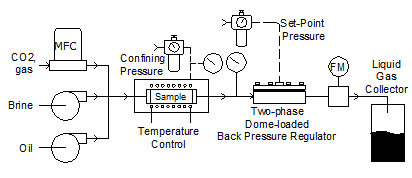
Schematic of a typical core flooding test setup
The ideal BPR can hold the reactor pressure at a very stable pressure even as the flow rates vary from near zero nanoflow up to high flow rates (typically tens or hundreds of ml/min). The BPR must also provide precise control for two-phase gas and fluid control.
Pore Pressure Transmission Testing
Pore pressure transmission (PPT) testing is used in petrochemical research to determine the effectiveness of oil drilling fluids. A PPT device simulates the pore pressure generation that occurs inside shale rocks during drilling processes and measures pore pressure changes over time. The test results help guide drilling fluid design and the selection of optimum operational conditions for improved drilling efficiency.
Upstream pressure control is an important part of the PPT design because the primary variable being monitored in the experiment is the pressure change at the downstream end. As such, any deviation in upstream pressure will have a correlated effect on the test results. In order for the results to provide meaningful information, downstream pressure measurements need to be recorded to a 1% accuracy.
Equilibar U10L has been used successfully in such testing as told in this case study from the University of Aberdeen at right.
Request a Quote Download Brochure
Equilibar High Pressure Regulators for Core Tests
Several Equilibar® Research Series BPRs are designed to meet the demanding requirements of high pressure control applications in the coretest . Equilibar Research Series products hold stable pressure across a wide range of flow rates and can easily handle liquids, gases, or even multi-phase flow.
Equilibar® BPRs are 1:1 dome-loaded, meaning that a pilot pressure must be supplied to the dome of the BPR equal to the desired setpoint. This pilot pressure can be controlled by a manual gas pressure regulator or by an electronic pressure regulator for computer automation.
The Equilibar’s dome-loaded, multiple orifice design offers instantaneous control and exceptional precision.
U10L Ultra Low Flow Back Pressure Regulator
The UL series is a departure from the multiple orifice design as it uses a single outlet orifice design. An Equilibar application engineer may recommend the UL Series in certain ultra-low flow applications, including coretest applications. The U10L is specifically designed to withstand pressures up to 10,000 psig (690 bar(g)).
H10P Back Pressure Regulator
With a pressure rating up to 10,000 psig (690 bar(g)), the H10P is often used in reservoir core analysis applications. These units are available in NPT, HIP-style, Speed-bite-style, and HPLC-style port connections. Diaphragms are available in SS316, Hastelloy, or PEEK to reach the high coretest application pressure. The H10P is one of Equilibar’s patented multi-orifice designs, in which more orifices open up as needed to accommodate increasing flow requirements. This design offers the highest possible precision in multi-phase flow applications.
Request a Quote Download Brochure
Mity Mite Back Pressure Regulator
Originally introduced by Grove in the 1960’s, the Mity Mite back pressure regulator has been a staple of many fluid control applications, ranging from amateur rocketry to petrochemical research applications including core testing. However, in 2015 customers were faced with the total withdrawal of these products from the market.
For legacy applications that require an exact drop-in replacement, Equilibar is able to meet your needs with Mity Mite replacement diaphragms and back pressure regulators.
While Mity-Mite and the Equilibar back pressure regulators work in a fundamentally similar way, the unique design of the Equilibar regulator gives it much more sensitivity. In addition, spare parts for Equilibar BPRs are available in as little as 24 hours.
Request a Quote Download Brochure
Back Pressure Regulator for 20,000 psi
Equilibar offers several models of back pressure regulators rated and tested for use up to 10,000 psi. The Equilibar design is highly scalable and has been successfully scaled from 1000 psi in early models up to the 10,000 psi models we offer today. We have also worked with clients to develop a beta version of a 20,000 psi model that has performed well and we are glad to offer this as a custom product.
Equilibar currently has hydrostatic pressure shell testing capabilities to 50,000 psi. This range is adequate to confirm existing 10,000 psi design drawings through actual empirical testing to 4X overpressure, but it is not high enough to perform a design verification to 4X for a 20,000 psi design. In addition, we perform operation testing on every regulator we ship at 1.5X the maximum operating pressure differential. Our current operation test apparatus allows us to perform these tests for models up to 10,000 psi, but not up to 20,000 psi.
However, our engineers are happy to discuss partnering with you to prove a scaled up Equilibar regulator design for your specific application. Please contact us for further information.