How do pressure and vacuum play a role in semiconductor manufacturing?
Pressure and vacuum regulation play a key role in several steps during semiconductor and microchip manufacturing from pressure control of gases to vacuum control for wafer handling. Equilibar® precision back pressure regulators (BPRs) and vacuum regulators (EVRs) are used for a variety of semiconductor fabrication processes because of their extreme accuracy, fast response and versatility to handle specialty gases. Below is a subset of applications where Equilibar valves shine.
Pressure control in inert gas delivery systems
Semiconductor manufacturing requires inert high-purity gases to protect wafers during each step, reducing impurities, preventing contamination and improving yield. In addition to operating at tight pressure and flow specifications, a well-designed inert gas system is safe, easily automated and easy to maintain. Equilibar BPRs have all the qualifications to be valuable in a semiconductor gas delivery system.
- The unique Equilibar design with a flexible diaphragm as the only moving part allows the BPRs to be extremely accurate and responsive, especially in automated applications.
- Equilibar engineers understand the complex requirements for valves used in high purity gas control and will design a solution specific to each application.
- When requested, an ASTM G-93 Oxygen cleaning service is available to maintain purity.
- Equilibar valves come in sizes that can accommodate a range of flow and pressure conditions to meet the process needs.
- A variety of connection types are available depending on customer preference: VCO, VCR, SAE, Swagelok, and more.
- With its simple design, an Equilibar BPR can be cleaned and maintained in minutes.
Vacuum holding semiconductor wafers
Sensitive vacuum tables are used to hold semiconductor wafers in place during inspection or other processes. Vacuum table applications often pose a difficult pressure control challenge, especially when they involve thin membranes or silicon wafers being placed on and off the table. Flow rate fluctuates rapidly as the number of open holes in the table varies when wafers are placed on and off the table during processing. Such a swing in flow rate would cause an unregulated system to fluctuate in vacuum pressure, resulting in changes to suction force on the sensitive parts and possible damage.
The solution is to use a vacuum regulator capable of responding quickly to rapid system changes. The Equilibar EVR is designed to immediately open or close when it senses a disturbance in flow, resulting in precise vacuum table pressure control. Below is a video demonstrating the responsiveness of the Equilibar EVR in this application.
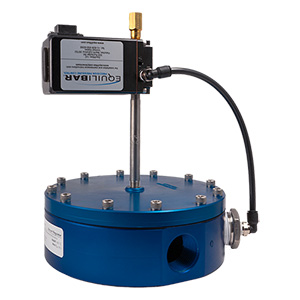
Equilibar vacuum regulator made of anodized aluminum with an electronic pilot regulator
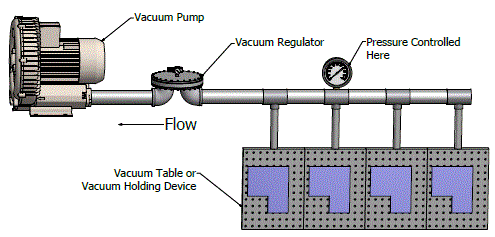
Equilibar vacuum regulator is used to maintain control in vacuum holding table
In addition to vacuum holding, Equlibar EVRs are used in vacuum packaging of products, and pick and place suction cup control. In pick and place control, the EVR reaches the desired suction pressure quickly, immediately compensates for different pick and place modules coming on and off line, and remains on target if a plunger misfires.
Deuterium gas control in semiconductor annealing
Deuterium gas is a heavier, stable isotope of hydrogen and is used in semiconductor fabrication to improve longevity. During deuterium annealing, standard protium hydrogen atoms are replaced with deuterium. The Si-D bond is less prone to vibrational excitations than the normal Si-H bond, making it more robust and improving the durability of the semiconductors.
Precision pressure control in the annealing chambers is important during the process which is carried out at high temperatures and relatively high pressures. Equilibar BPRs have an excellent track record controlling processes in these conditions.
Cooling loops for semiconductor manufacturing:
Liquid cooling loops are used in a variety of different semiconductor manufacturing systems, but the most challenging is often thermal testing of processors. In the thermal test process, a newly manufactured chip is subjected to stress testing in a variety of different conditions, requiring precise control at several temperature setpoints throughout the test procedure. Other processes like lithography or etching require temperature stability of ±0.1 K or greater.
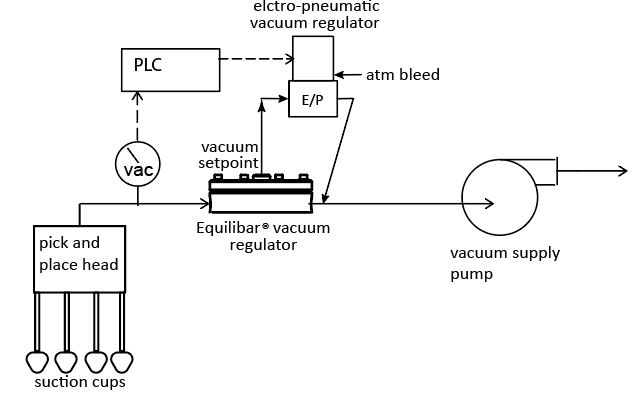
Equilibar EVR-GSD is used to control pick and place suction cups
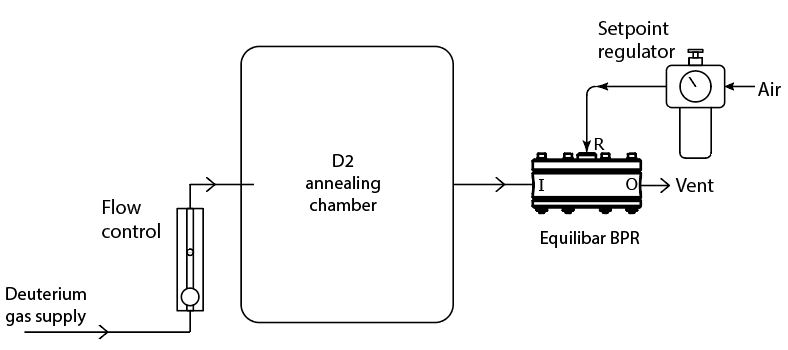
An Equilibar BPR controls annealing chamber pressure during deuterium-protium exchange process.
Regardless of the specific process requiring liquid cooling, Equilibar valves offer several advantages over traditional control valves or BPRs. The wide Cv range of the Equilibar valve allows for stable control across a wide range of operating conditions. In systems where one cooling loop feeds multiple processes/machines, this is particularly important as the amount of flow being recirculated back to the pump can vary dramatically depending on the number of machines online. With turndown ratios of 100:1 or greater, Equilibar valves allow for precise control as this flow varies. Additionally, the simple design of the Equilibar BPR allows for easy maintenance, with most valves being able to be fully rebuilt in the field within a matter of minutes. The multi-orifice design also prevents cavitation damage that is a common concern for single seat valves in high dP liquid systems.
Equilibar valves can also be used to directly control flow or even temperature, when paired with electronic controls and feedback from an external flow meter or temperature sensor.
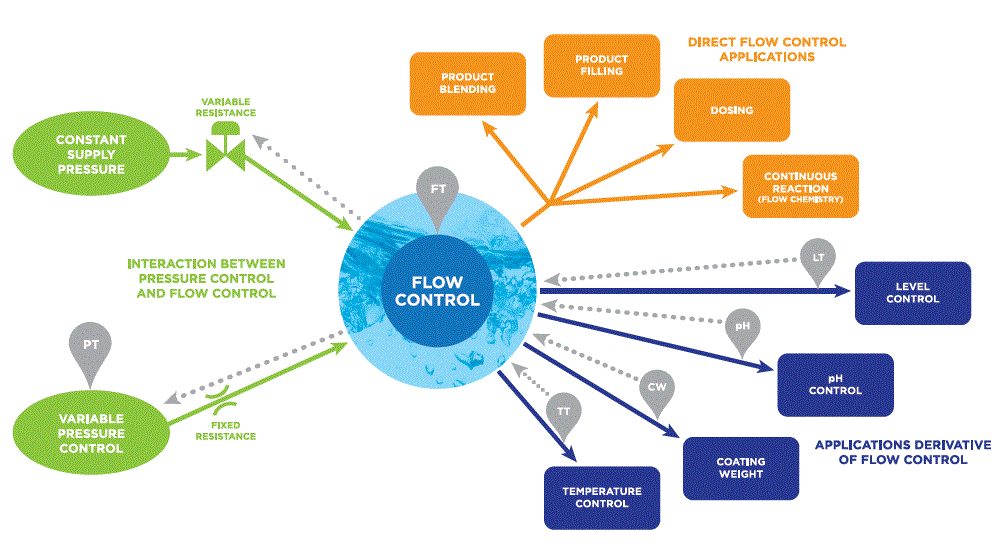
Graphic representation of the interaction of pressure and flow control on process control variables.
Other semiconductor related applications where Equilibar products can help
- Corrosive etchant flow control in lithography
- Imaging chamber pressure control (lithography)
Equilibar engineers are constantly looking for new ways to address demanding customer challenges. If you have an application in the semiconductor industry that requires fluid control, contact our engineers to discuss your application
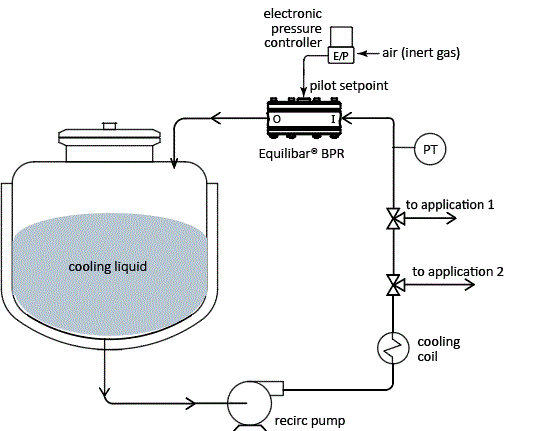
Liquid cooling loop with multiple application ports controlled by an Equilibar back pressure regulator