NOTE About this page
Equilibar valves are used today to solve many complex flow control applications. This page shows the early learnings of applying an Equilibar valve to control flow and is retained for historical archive purposes.
For the latest information about Equilibar flow control valves
visit our updated flow control page.
Equilibar® control valves provide precision control across a wide range of flow rates for gases, liquids and mixed phase fluids. The unique dome loaded multiple orifice design responds quickly to changes in upstream and downstream process disruptions to maintain its setpoint.
Equilibar valves can be an excellent solution for closed loop flow control in complex applications that cannot be solved by traditional flow control methods. Some of the demanding applications where Equilibar valves provide improved performance include:
- Flow coefficient (Cv) ranges wider than traditional valves (>100:1)
- Extremely low DP and extremely high DP
- Two-phase, phase-change and supercritical states
- Continuous flow chemistry
- Sanitary applications
How the Equilibar Flow Control Valve Works
Equilibar valves are dome loaded and pilot operated, meaning a gas is supplied to the dome (top) of the valve through a pilot controller to set the setpoint for the process. A direct sealing diaphragm in the dome covers a field of orifices and adjusts its position to allow flow through the orifices to maintain the desired setpoint.
The Equilibar flow control valve is set up with an electronic pilot pressure controller and a flow meter in a control loop. (See schematic at right). A proportional-integral-derivative (PID) controller monitors input from a flow transmitter (FT) and adjusts the pilot pressure to control flow. An electro-pneumatic transducer (E/P) translates the electronic signal from the PID into a pressure signal for the pilot controller. Flow is decreased by raising the pilot pressure and increased by lowering the pilot pressure. The system works best with a stable supply pressure.
This video demonstrates how it works
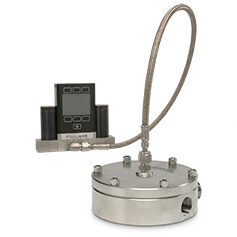
Equilibar GSD valve with electronic pilot controller for automated flow control
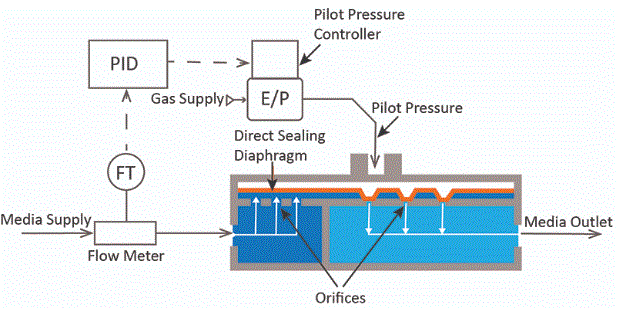
How Equilibar’s Direct-Sealing Diaphragm Valve works to Control Flow
Reasons to Consider an Equilibar Back Pressure Regulator for Flow Control
Operates Across a Wide Range of Flow Coefficient (Cv)
One characteristic of traditional flow control valves is that of limited flow range (or the max/min ratio of effective Cv). Most control valves operating in research and process industries are limited to between a 10:1 and 15:1 ratio. An Equilibar back pressure regulator can easily operate in a Cv range greater than 100:1.
Read our article in Flow Control Magazine at the right which describes a specific customer application with the range of flow Cv from 1E-5 to 2E-2 and a turndown ratio of approximately 2500:1.
Learn more about Equilibar’s flow control valve with wide flow range.
Controls Multi-Phase Fluids
The unique design of the Equilibar® back pressure regulator enables it to handle two-phase or mixed-phase flow streams while maintaining high precision. This can include gas/liquid processes, water/oil flow streams, or supercritical fluids.
Traditional back pressure regulators use a single annular valve seat, often very small, so that when slugs of liquid flood the valve throat, volumetric flow rate drops suddenly as the denser fluid is accelerated through orifice. This momentary reduction in volumetric flow disrupts the stability of the upstream process pressure.
The unique Equilibar technology uses a direct sealing diaphragm over multiple orifices to control the pressure drop. The supple diaphragm can vary its proximity to the orifices nearly instantaneously to adjust to the varying valve coefficient (Cv) requirements of the various phases.
Read our article in Flow Control Magazine at right which describes a specific customer using an Equilibar BPR for flow control of multi phase fluid.
Isolates from Downstream Pressure Changes
An Equilibar fluid control valve provides a buffer against changes in downstream pressure. Equilibar valves will automatically adjust to keep its inlet pressure at setpoint regardless of process changes at the outlet port. When using a traditional flow control valve (FCV), any change in downstream pressure will require a PID control adjustment to remain stable. Read more about Equilibar’s injection flow control valve resistant to downstream pressure fluctuations.
High Resolution
Equilibar dome-loaded valves have ultra high resolution, zero hysteresis and zero dead-band. This can be useful where traditional control valve deadband (or “stiction”) do not have adequate precision. Small adjustments may be made to the differential pressure resulting in high resolution process control. See details for high resolution flow control application in temperature control.
Demanding Service Conditions
Equilibar BPRs have only one moving part and are therefore easily configurable for the following severe and demanding service conditions:
- high temperatures – Case Study: Equilibar Valve Controls Flow for High Temperature Vinyl Acetate Monomer Reactor
- highly corrosive acids
- sanitary processes
- ultrapure requirements
Continuous Flow Reactions
Controlling pressure in continuous flow chemistry is important for phase control, residence time, reaction speed and equilibrium management. For instance, reaction temperature is a key component in reaction efficiency but at high enough temperatures, a reagent can reach boiling point which negatively impacts the reaction. Controlling reaction pressure by adding a back pressure regulator to the outlet of the reactor can prevent reagent boiling.
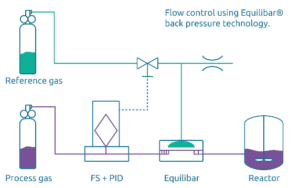
Our Northern European Partner, Pressure Control Solutions, describes how an Equilibar valve can control ultra low flow rates. Read their blog here.