5 reasons to use the Equilibar electrolyser pressure control solutions
1. Equilibar regulators have a wide Cv turndown exceeding traditional globe or ball valves
Equilibar BPRs are used to control electrolysis processes at a range of flows and pressures, high or low, with extreme precision. The unique multi-orifice design of Equilibar BPR allows for stable pressure control across a wide Cv range (10,000:1).
2. Equilibar valves can easily process multi-phase fluids
Equilibar valves, with their multi-orifice design, can maintain pressure even with mixed phase (liquid-gas) flow or varying pressures on the outlet of the BPR.
3. Equilibar back pressure regulators can handle very low or high dP across the valve
Oftentimes in production electrolyzer systems, it is advantageous to have minimal pressure drop across the BPR, with the pressure downstream being as high as possible to reduce the need for pumping up the gas to a higher pressure for storage or usage. Equilibar BPRs, when sized properly for the required Cv, can maintain stable pressure control with minimal pressure drop across the BPR. In contrast, traditional control valves and spring-loaded BPRs often have difficulty operating with a very small dP across the valve.
If instead, the system requires a large pressure drop across the valve, which would normally cause cavitation or otherwise damage traditional single-seat valves, Equilibar BPRs can also handle that scenario. The unique throat geometry of the Equilibar valves with multiple parallel flow paths, has proven to avoid cavitation issues (both pitting and noise).
4. Equilibar valves can be made from materials to handle aggressive conditions
The simplicity of the Equilibar design also allows us to easily tailor the materials of construction for the challenges of high pressure electrolysis. The regulator body can be machined from high nickel containing alloys like brass, bronze, or Monel to be used with high pressure pure oxygen. For alkaline electrolysis, we can use polymer diaphragm materials like PTFE or PEEK, O-ring materials like Viton, EPDM, or Kalrez, and bodies made from alloys like Hastelloy, Inconel, or Monel. Equilibar valves can be cleaned for oxygen service upon request as well. For systems where leaching of metal ions into a DI water supply is a concern, our valves can be passivated as well; alternatively, custom valves with a polymer flow path (eg. PEEK) can be made with a metal outer cradle/shell for safety.
5. The Equilibar back pressure regulator adjusts instantaneously to maintain pressure
The pressure control of the Equilibar regulator is not reliant on an external transducer and PID loop, so the BPR reacts nearly instantaneously to changes in flow and adjusts its Cv accordingly to maintain the desired pressure. This precise pressure control is particularly important when dealing with sensitive proton exchange membranes which will rupture if the dP across them is too high.
Contact An Engineer for Details
Ways to use Equilibar back pressure regulators in electrolysis systems
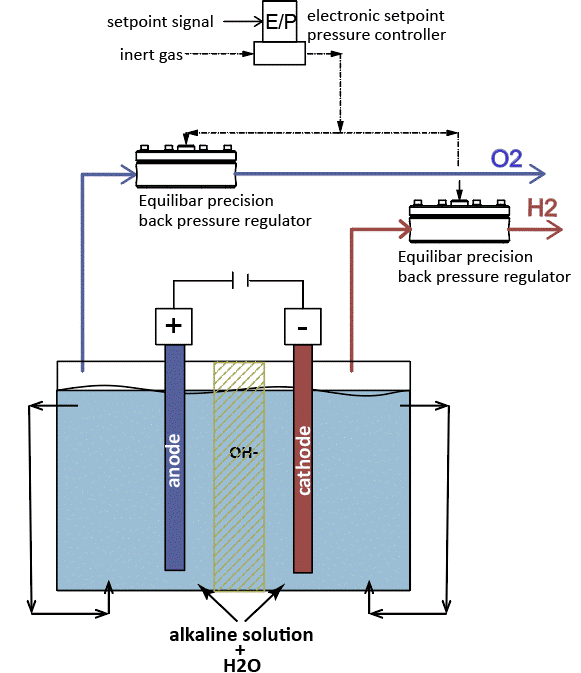
Alkaline electrolysis using Equilibar back pressure regulators to control O2 and H2 gas pressure.

Equilibar GSDM8 back pressure regulator for higher flow electrolyzer pressure control
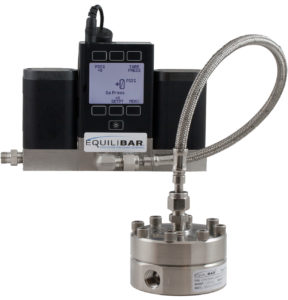
Equilibar LF back pressure regulator for low flow electrolysis pressure control
PEM Electrolyzer differential pressure control
Equilibar BPRs can be used to control the outlet gas pressure on oxygen and hydrogen lines coming from a PEM stack. By putting an Equilibar BPR on the gas outlet of the anode and cathode side of PEM stack, precise dp (differential pressure) can be maintained across the stack at all times. Why use an Equilibar BPR for PEM stack pressure control? Because an Equilibar BPR can control high pressures, can process high temperature and mixed-phase fluids, and is easily integrated into electronic control system with an E/P or I/P pilot regulator.
Contact An EngineerPEM Electrolyzer control downstream of separator
Equilibar BPRs can also be used downstream of a separator or liquid dropout. In some systems it is advantageous to put the BPR downstream of a separator, as opposed to directly downstream of the PEM stack, so that pressure in the DI water loop is maintained. Advantages of using an Equilibar for this setup are:
- Equilibar BPRs can handle high dP across the valve without causing damage or poor performance issues.
- The Equilibar BPR will isolate the system from downstream pressure fluctuations (e.g. potentially varying gas pipeline pressure in production facility) and maintain stable control even as this outlet pressure varies.
Use a single setpoint on 2 Equilibar BPRs to maintain PEM stack pressure differential
The dome-loaded control of our BPRs also means that that it is possible to control the pressure on both the cathode and anode side of the electrolyzer with one pilot pressure regulator connected to the dome of two BPRs, ensuring that the pressure on both sides of the PEM closely match each other.
When pressure on the O2 and H2 streams need to be controlled at the same pressure, this single setpoint dome pressure setup is very handy. This also works well for electrolyzer depressurization during emergency shutdown procedures.
Read more details about our completely mechanical solution for depressurization during emergency shutdown operations and contact us to discuss your electrolysis application.
Discuss Your ApplicationRelated electrolytic reactions: Chlor-Alakali
Chlor-Alkali electrolysis combines salt and water to generate chlorine, caustic soda and hydrogen (2 NaCl + 2 H2O = Cl2 + 2 NaOH + H2). In Chlor-Alkali electrolysis, the anode and the cathode are separated by an ion-exchange membrane. Hydrogen gas forms at the cathode and chlorine gas forms at the anode. The NaOH caustic solution remains and is collected and often concentrated.
Case Study: Equilibar technology used for electrolysis to generate oxygen in space
Flow cell electrolysis, which is used for spaceflight applications, uses a flowing water electrolyzer to generate enough oxygen from water to keep up with the crew’s metabolic requirements. Many of the current electrolyzer designs require a downstream gas-liquid separation process, presenting challenges in a microgravity environment. One complication is two-phase flow caused by bubble generation in the electrolyzer. Researchers at the University of Colorado at Boulder proposed an alternative electrolyzer configuration and built a prototype using an Equilibar® vacuum regulator.
Contact An EngineerAbout Equilibar back pressure regulators
The Equilibar® back pressure regulator is dome-loaded and, with its novel multiple orifice design, delivers instantaneous reliable control in the most challenging applications. The dome-loaded design means it requires a fluid (typically air or nitrogen) pressure applied to the dome of the BPR matching the desired inlet pressure. This setpoint pressure can be manually or electronically controlled. Learn how Equilibar back pressure valves work.
Our team of experienced engineers offer detailed guidance in choosing the pressure control products for a specific condition. Special considerations are taken into account for oxygen rich processes seen in electrolysis.
Contact an Equilibar engineer to discuss your application in more detail.
Electrolyzer Technology
Popular water electrolysis technologies: Alkaline Water Electrolysis (AWE), Proton Exchange Membrane Electrolysis (PEM), and Solid Oxide Electrolysis (SOEC).
Alkaline water electrolysis is the oldest and most advanced methodology for water separation. In AWE, the electrodes are immersed in an alkaline solution where the ions are transported and separated. PEM electrolysis systems use a solid membrane and typically operate at a higher pressure than alkaline systems, giving them the advantage of minimizing the need for a second stage mechanical compression to pressurize hydrogen for storage. SOEC electrolysis also uses solid membranes but are made of ceramic and run at high temperatures.
In all electrolysis technology designs, pressure regulation of the O2 and H2 gas streams is extremely important to the efficiency and life of the electrolyzer.