Ammonia is a potential transport and storage vector for hydrogen that has shown great promise. Ammonia is comparatively easy to store in liquid form and the infrastructure for transporting massive quantities already exists within the agriculture industry. Once the ammonia is transported to its destination, it can be converted to hydrogen via ammonia cracking.
How Equilibar regulators are used in ammonia cracking for hydrogen production
In the ammonia cracking process, the ammonia is heated to an elevated temperature, typically in the range of 600-950 °C, in the presence of a metal catalyst. The ammonia molecule (NH3) then decomposes into nitrogen and hydrogen. Equilibar® regulators are uniquely suited to controlling pressure in cracking setups like this.
Contact UsA typical setup for ammonia cracking closely resembles a pyrolysis system and a portion of the produced hydrogen may be fed back into the burner heating the reactor, as in the schematic below.
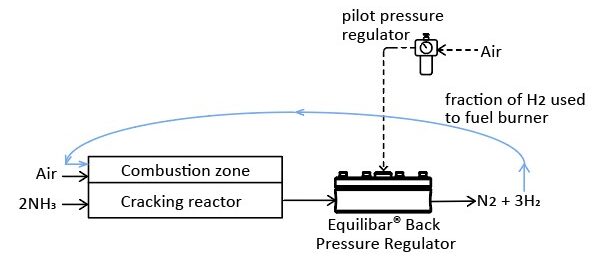
Equilibar back pressure regulator used in ammonia cracking reactor
While most control valves downstream of these cracking reactors are not subjected to the full reaction temperature, Equilibar BPRs have options to customize for high temperature using elastomer O-rings for service up to 327°C; graphite gasket seals for use up to 450°C ; and up to 648°C with metal c-rings.
Another valve design challenge is the resultant gas stream coming from the cracking reactor that may contain trace amounts of non-decomposed ammonia. For use downstream as a back pressure regulator (BPR) or flow control valve, Equilibar’s simple design allows the soft seals in the valve (diaphragm and O-rings) to be easily tailored to the application’s chemical compatibility requirements. There may also be liquid ammonia droplets in the produced gas stream, which normally result in pressure fluctuations when traditional single seat valves are used. But the multi-orifice design of Equilibar valves allows them to maintain stable control even in the most demanding two-phase liquid-gas flow applications.
Equilibar BPRs are also easily automated by using an electronic pilot regulator to control the reference pressure above the diaphragm. This allows for stable control and remote monitoring without the need for an operator or technician to manually intervene.
Application Spotlight: Ammonia Cracking on Container Ships
An increasingly common use-case for ammonia-to-hydrogen systems like this is on large container ships. The hydrogen produced by ammonia cracking may be used to generate electric power for the ship via a hydrogen fuel cell or may be directly injected into diesel engines as a means of reducing carbon emissions and the amount of diesel consumed.
Equilibar valves are commonly used in test stands for both fuel cells and fuel injectors but may also be used in these full production systems delivering the same benefits over traditional control valves.
Summary: 5 Benefits of using Equilibar valves in ammonia cracking service
- Equilibar valves can be used at high temperatures, up to 648°C with all metal seals
- Wide variety of sealing options for corrosive conditions
- Ability to handle mixed-phase liquid-gas flow without degrading accuracy
- Wider operating Cv range than traditional control valves
- Easier rebuild process and fewer internal components than traditional control valves – lower overall cost of ownership throughout the lifetime of the valve