Pressure Control in Supercritical Extraction
Supercritical fluids offer many advantages for the extraction process, particularly when using supercritical carbon dioxide (SCO2). When SCO2 is used to extract essential oils from botanicals the final product will remain free from the potentially harmful solvents used with older extraction technologies. Carbon dioxide is relatively inexpensive, widely available, and can be recycled and reused indefinitely. The schematic shows a typical batch extraction process. The system is initially charged with liquid CO2 from a commonly available bottle (with siphon tube). The CO2 is mixed with any desired co-solvents that may be required to assist in extracting the targeted media. Ethanol is often used as a co-solvent as it offers many of the same low toxicity benefits of carbon dioxide.
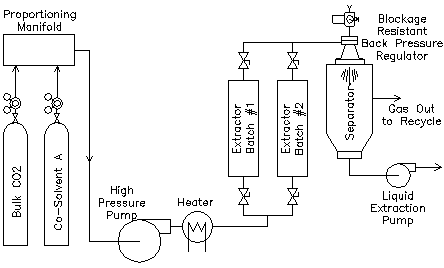
Supercritical Extraction Batch Schematic
A pump is used to increase the pressure of the carbon dioxide to a point above the supercritical pressure. A typical system might run its extraction pressures anywhere between 1800 and 5000psi. This pressure can be adjusted to allow greater selectivity in which media is targeted to be extracted. A heater is used to increase the temperature of the CO2 to push it past the sub critical point and into the supercritical stage. The supercritical extraction then occurs as the SCO2 and co-solvents move through the media in one of the two batch extractors. After exiting the extractor the supercritical fluid pressure must be let down to a pressure that can be tolerated by the construction of the separator vessel and is at a low enough pressure to ensure that the entrained essential oils will be allowed to drop out completely.
This pressure let down is best achieved by using a back pressure regulator (BPR). The back pressure regulator performs two functions. The first is maintaining the extraction vessel pressure at the desired supercritical extraction pressure independent of the flow system rate. Secondly the BPR creates the pressure drop required to step the supercritical extraction fluid pressure down to the level required by the separator. The expansion of the supercritical fluid during this pressure let down stage is often problematic. The Joules-Thompson effect causes a dramatic temperature drop to occur which can lead to ice formation that will block the internal passages of the BPR.
The Equilibar BR Series back pressure regulator uses a patent pending technology to resist the build up of ice in its internal passages. This technology is due to the innovative mechanical workings of the regulator and does not rely on external heating. The design also resists blockage from oils that have become highly viscous due to the extreme cold of the expanding gasses. See the video to the right. After the pressure let down step the targeted oils are separated and the CO2 and co-solvents may be removed for recycling. The schematic shown has been simplified for illustration purposes.
Request a Quote Download Brochure
Accurate Control for Precision Extraction Pressures
The Equilibar BR series regulator controls pressure very accurately and is able to hold the extraction pressure precisely at the required set point regardless of fluctuations in the system flow rate or variations in the system temperature. This allows for more precise targeting of the desired extract. The BR series can achieve this precision because it uses the Equilibar patented innovative direct diaphragm sealing technology coupled to internal passages designed to resist the formation of ice blockages. A responsive flexible diaphragm is the only internal moving part. The diaphragm is nearly frictionless in its movement and does not have accuracy robbing hysteresis and “stiction” (static friction) like traditional needle, ball, gate, or butterfly regulating valves have. The diaphragm has very low mass and will respond to changes in system flow rate within milliseconds.
Rugged Design Handles Extreme Temperatures and Chemistries
The BR1 body is manufactured from bar stock stainless steel 316L for maximum durability and chemical compatibility. The flexible diaphragm material is carefully selected to match your application temperature and media. Temperature ranges to 325 C can be directly controlled with the BR1. While typically not required, this does allow for external heat tracing to be directly applied. The availability of PTFE and Polyimide/Kapton diaphragm materials means that almost all supercritical extraction fluids and co-solvent combinations can be regulated with the BR1.
Learn more about using fractional distillation to separate multiple extracts at multiple pressures
Learn more about carbon sequestration and other supercritical CO2 applications
Video Shows an Equilibar BR Regulator used in Supercritical Batch Extraction
This video demonstrates how a BR supercritical back pressure regulator can be used for supercritical extraction. In this laboratory setup, the reactor is extracting oil from basil leaves. Additional footage shows the BR valve’s excellent anti-blockage capabilities for supercritical fluid systems which oftentimes experience oil and ice buildup and blockage.
The Equilibar BR blockage resistant back pressure regulator is shown above with a flange connection on the discharge port, allowing the output of the regulator to discharge directly into the separator vessel.
Case Study: Plant matter extractor uses Equilibar Blockage Resistant (BR) back pressure regulator to maintain extraction pressure. Ice and extraction oils discharge from the BR directly into the separator vessel with no blockage issues.
Video: Watch as the Equilibar BR regulator easily sheds the ice formations to remain blockage free. The bottom plate has been removed for easier viewing