How are Equilibar Valves Useful in fuel Injector pressure control?
While Equilibar back pressure regulators (BPRs) have been used for pressure control in automotive test stands for over a decade, one increasingly common application for our valves has been pressure control for fuel injector test stands.
Fuel injector test stands or test benches typically involve the control of both the pressure upstream (p1) and downstream (P2) of the injector to ensure that it outputs the desired flow with a given pressure differential. The pressure upstream of the injector is generally provided by a high pressure fuel rail with a pressure reducing regulator (PRR) upstream. On the downstream side, depending on the setup, there may be a BPR on each injector to test them all for a variety of discharge pressures (fig 1) or a shared accumulator (fig 2) if they are all being tested at the same discharge pressure.
Equilibar BPRs work great for fuel test systems like this as they are easily automated with an electronic pilot regulator and respond immediately to changing conditions or setpoints. Additionally, the wide Cv range and ability to maintain stable pressure control with mixed phase liquid-gas flow allows them to be used in systems which would normally require 2 or more control valves to cover a similar range. In terms of material compatibility, our simple design with a diaphragm as the only moving part allows us to tailor our diaphragm and o-ring materials to each application’s chemical compatibility, temperature, and pressure requirements.
Application Spotlight: Hydrogen fuel injection
As part of the recent global growth of hydrogen infrastructure, hydrogen fuel enhancement for internal combustion engines has been a topic of increased interest. By injecting high pressure hydrogen into a diesel or natural gas engine, both an increase in fuel economy and significant reduction in CO2 emissions can be achieved.
Equilibar BPRs work just as well for hydrogen injector test stands as they do for traditional fuels. For pure hydrogen gas, Equilibar also has electronic PRR options such as the EPR series and HP-ERC that could be used upstream of the H2 injectors as well.
Contact an Equilibar applications engineer to discuss your specific test stand requirements.
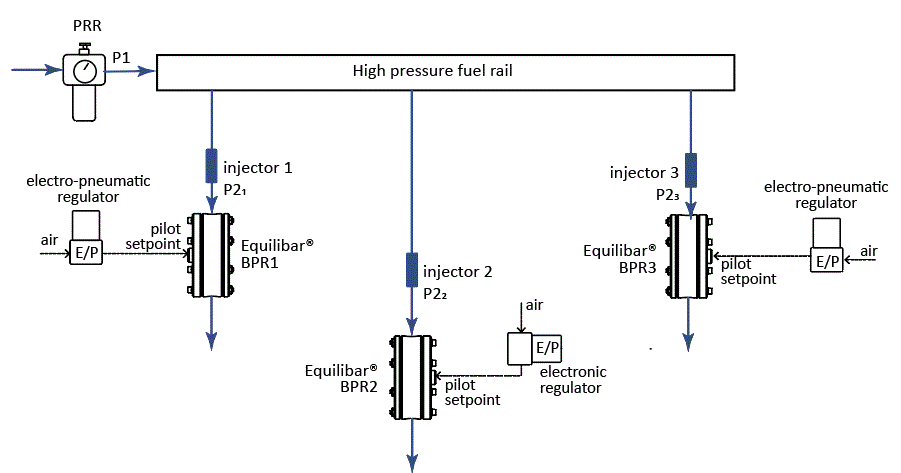
Fig 1: Fuel Injector test bench with a BPR on the outlet of each injector, allowing for individualized control of the discharge pressure (P21-3).
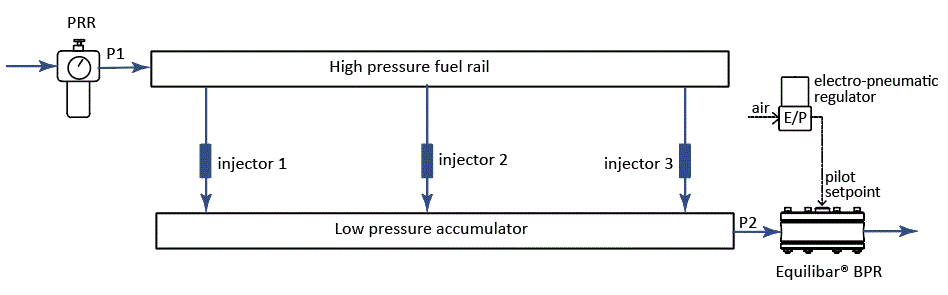
Fig 2: Fuel Injector test bench with one BPR controlling the discharge pressure (P2) for all injectors in a shared accumulator.
Equilibar BPRs do not rely on any PID or control loop for back pressure control, only on a force balance across a flexible diaphragm. This means that the BPR can respond nearly instantaneously to changes in flow, as any change in flow/pressure upstream will create a force imbalance across the diaphragm, raising or lowering the diaphragm. This allows for simple, stable pressure control with the BPR dynamically adjusting its Cv as needed. Compared to a control valve paired with an external transducer and PID controller, there are no issues with lag while the control loop catches up to transient fluctuations.
Equilibar GSD Stainless Steel Back pressure regulator with QPV electronic pilot controller