What are the design considerations for a pharmaceutical API tank blanketing system?
API pharmaceutical processing has some added complexities over biopharma processing that should be considered. For instance, solvents are commonly used and require partial pressure control to suppress evaporation. Additionally, high molarity buffers can sometimes be too aggressive for stainless steels, requiring the use of exotic metals for component construction like Hastelloy. So, in addition to the quality of the nitrogen gas source, the process parameters to consider in API blanketing are
- flow rate of nitrogen gas
- pressure control range
- Automation requirements
- chemical compatibility with volatile gases
- cleanability requirements
- ATEX requirements
Tank blanketing applications require precise flow and pressure control of nitrogen gas into and out of the process tank to keep the pressure inside the tank at the desired setpoint. A typical nitrogen padding system supplies nitrogen to the tank with a pressure reducing valve (PRV) or tank blanketing valve until it reaches the pressure setpoint. When conditions change and tank pressure exceeds the setpoint, blanket gas is removed from the tank using a back pressure regulator (BPR) or “de-padding” regulator. Below is a schematic showing how it might be designed.
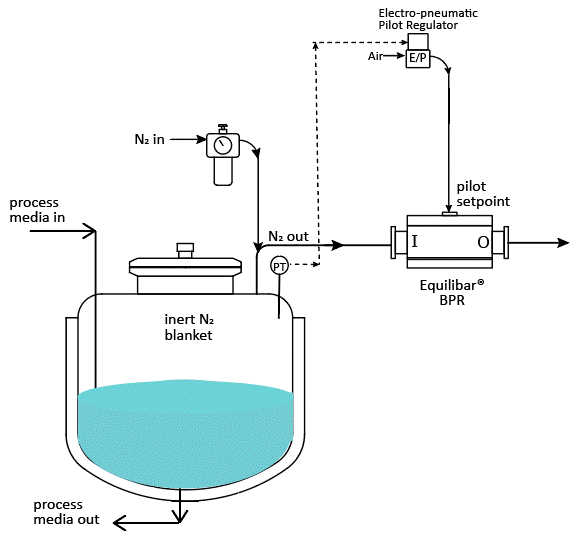
Schematic example of API tank blanketing
Equilibar Back Pressure Regulators are an excellent solution in API tank blanketing applications
Equilibar back pressure regulators are widely used in tank blanketing applications to relieve excess pressure in the tank. Why are Equilibar BPRs well-suited for tank blanketing in API?
- They can be designed to specifically meet the parameters required in API pharmaceutical processing.
- Hastelloy material can be used for cases where corrosive volatile gases in the API process could be in the gas stream with the nitrogen.
- The Equilibar valve can provide significantly lower control ranges as compared to traditional spring solutions, offering users ultra-low pressure ranges (inWC/mbar) without exhibiting over-pressure behavior
- Design options are available if CIP or SIP cleanability is required.
- Equilibar BPRs can be controlled manually or electronically.
- The pilot setpoint regulator for the BPR can be chosen based on ATEX considerations. It can also be placed in a location outside an ATEX area.
- The multiple orifice design and flexible diaphragm allow the Equilibar BPR to adjust instantaneously to changes in pressure inside the tank without hysteresis or cracking pressure.
- Equilibar BPRs work across a wide range of flow rates and are often chosen over traditional valves for their Cv rangeability.
Contact an Equilibar application engineer to discuss your tank blanketing application.